Anche i migliori test di laboratorio non sono in grado di riprodurre le condizioni reali e i test nei processi attivi sono talvolta inefficienti e persino impossibili. Per testare gli strumenti di misura in condizioni e configurazioni specifiche, WIKA ha costruito negli USA una propria unità di processo a grandezza naturale, completa di reattore e forno a gas.
Oltre il semplice test: ecco perché WIKA ha costruito un’unità di processo a grandezza naturale
I laboratori WIKA per i test e la progettazione sono tra i migliori al mondo. In questi ambienti controllati, testiamo attentamente e metodicamente la nostra strumentazione che verrà poi utilizzata per la misura di temperatura, pressione, portata, livello e forza. In alcuni casi, commissioniamo a istituti terzi la convalida dei nostri risultati.
Tuttavia, i test di laboratorio non sono sempre sufficienti. Per certi processi, un ambiente simulato non è in grado di duplicare le condizioni reali.
Per gli strumenti di temperatura usati negli impianti di processo, l’ideale è effettuare i test presso un’unità attiva, ma gli svantaggi sono tempo, costi e praticità. Le raffinerie e gli impianti petrolchimici devono continuare a funzionare per rimanere redditizi, e i fermi impianti vanno limitati solo alla manutenzione e alle riparazioni. I test hanno luogo durante questi arresti programmati; infatti, alcuni test degli strumenti iniziano durante un turnaround (TA) e vengono lasciati in funzione fino al successivo. Il problema è che queste condizioni specifiche sono fissate per un lungo periodo, dal momento che i cicli di turnaround spesso durano quattro o più anni. Ciò richiederebbe un test molto lungo!
Inoltre, un test può richiedere azioni che sarebbero inaccettabili in una situazione reale. Per esempio, le termocoppie con fili spelati vengono martellate in piccoli fori praticati lungo le pareti del tubo del forno. Questo processo va bene in un ambiente di laboratorio, ma farlo in un’unità di processo attiva indebolirebbe la parete del tubo e creerebbe potenziali punti di rottura.
Per testare adeguatamente la gamma di termocoppie e altri strumenti di misura di WIKA, abbiamo ideato una soluzione in grado di combinare il meglio dei due mondi: un’unità di processo reale che i nostri ingegneri potevano avviare, arrestare e manipolare come necessario: il tutto senza dover scomodare nessuno nell’industria di processo.
L’unità di processo completamente funzionale di WIKA a Pasadena, Texas, è dedicata al collaudo degli strumenti e alla ricerca e sviluppo.
Centro di progettazione e di test WIKA
Prima di iniziare la costruzione di questa struttura di test di livello mondiale, i nostri specialisti hanno trascorso anni a consultarsi con diversi esperti del settore, licenziatari e utenti finali. Dopo aver ottenuto i loro commenti, ci siamo imbarcati in un’iniziativa multimilionaria per costruire un campus di ricerca e sviluppo di 557 mq (6.000 piedi quadrati) a Pasadena, Texas, non lontano dalle decine di raffinerie nel cuore dello Houston Ship Channel. Il fulcro di questo campus è un’unità di processo attiva a grandezza naturale che è stata progettata e costruita secondo le linee guida ASME e API.
L’unità, che è entrata in funzione a metà del 2019, lavora con fluidi che vanno dai liquidi ai vapori e ai fluidi a fase mista. E’ previsto anche un innovativo sistema di pareti del forno in grado di adattarsi a quasi tutte le condizioni di prova. La fornace da 9,6 milioni di BTU è in grado di replicare una vasta gamma di processi che avvengono in forni e reattori su larga scala.
Questa unità all’avanguardia permette alla nostra squadra di ottenere dati reali sulla completa gamma di strumenti di misura WIKA, compresi i seguenti prodotti ETM (electronic temperature measurement):
- Assieme termocoppia multipoint Flex-R® (modello TC96-R) di Gayesco
- Termocoppia WIKA V-PAD® tubeskin (modello TC59-V)
- Assieme termocoppia XTRACTO-PAD® tubeskin di Gayesco (modello TC59-X)
- Assieme termocoppia REFRACTO-PAD® tubeskin (modello TC59-R) di Gayesco
La struttura ci permette anche di sviluppare e testare la prossima generazione di strumenti destinati a raffinerie e impianti petrolchimici.
Test di durata reale in un’unità di processo reale
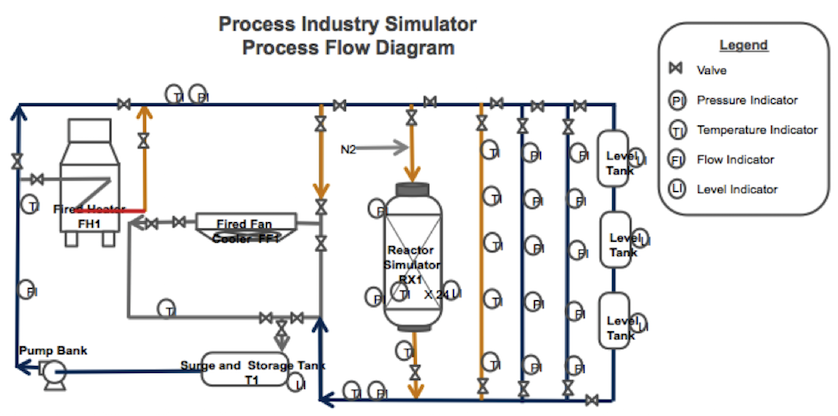
Con un’unità di processo a grandezza naturale e completamente funzionale, siamo in grado di eseguire una varietà di test e verifiche che prima non erano possibili. Oltre a mettere i nostri strumenti di misura in condizioni di lavoro reali, ora possiamo ricreare i problemi reali che le unità dei nostri utenti finali a volte sperimentano (maldistribuzione, punti caldi e canalizzazione, per citarne alcuni) e vedere come queste condizioni influenzano gli strumenti ETM.
A tal fine, la nostra struttura di prova è stata preziosa in due applicazioni: il monitoraggio delle condizioni del forno e la fluidodinamica computazionale.
Monitoraggio della condizione dei forni
Il monitoraggio delle condizioni dei forni (FCM – Furnace condition monitoring) è un processo attraverso il quale gli utenti raccolgono dati in campo per identificare le lacune nelle prestazioni. E’ quindi utilizzare queste informazioni per ottimizzare il posizionamento delle termocoppie e dei gruppi di tubi, così come per apportare altri miglioramenti operativi per ottenere prestazioni migliori.
Grazie all’FCM presso la struttura di prova, siamo in grado di:
- Condurre valutazioni in campo sulle condizioni termiche di un forno utilizzando strumenti diagnostici avanzati, tra cui le immagini termiche a infrarossi (IR) e altri strumenti
- Esaminare i risultati preliminari con gli specialisti di forni e ispezioni del cliente, i responsabili del funzionamento degli impianti e altri
- Rilasciare un rapporto sulle prestazioni del forno e le nostre raccomandazioni
- Fornire assistenza e consigli nella scelta della termocoppia, dei materiali e nella progettazione per una durata ottimale dell’unità
- Fornire e/o supervisionare l’installazione di sensori a termocoppia tubeskin per migliorare il monitoraggio della temperatura e migliorare le prestazioni del forno
- Impostare programmi di monitoraggio per riscaldatori critici.
Inoltre, il campus di ricerca e sviluppo è diventato un luogo naturale per la formazione pratica dei clienti per ottenere il massimo dai nostri strumenti di misura e dalle loro unità di processo. Queste migliori pratiche sono il risultato dell’FCM e includono come:
- Aumentare la capacità dell’unità attraverso l’ottimizzazione e l’eliminazione delle strozzature produttive del forno
- Migliorare l’efficienza energetica con una gestione ottimale della combustione del forno
- Usare le valutazioni di affidabilità per ridurre i fermi non programmati
- Ridurre i costi di manutenzione attraverso una migliore pianificazione del turnaround.
Fluidodinamica computazionale
Materie prime, catalizzatori, vapori, prodotti finali: tutti questi fluidi si muovono e scorrono. Ecco perché una raffineria o un impianto petrolchimico deve occuparsi di fluidodinamica computazionale (CFD – computational fluid dynamics), poiché questo processo simula, analizza e risolve i problemi di portata dei fluidi. La CFD usa l’analisi numerica, le strutture di dati e i calcoli al computer per creare modelli sulla portata dei fluidi e le sue interazioni con le condizioni di contorno.
Attraverso la modellazione CFD, possiamo comprendere fenomeni complessi con informazioni simultanee sul trasferimento di massa, quantità di moto e calore. Possiamo poi usare questi dati per pianificare test avanzati, convalidare e mettere a punto le condizioni limite e sviluppare soluzioni personalizzate.
Intuizioni derivate dai test
Da quando l’unità di processo ha iniziato a funzionare a metà del 2019, abbiamo eseguito una varietà di test utilizzando più di 50 sensori per il benchmarking, e abbiamo analizzato scansioni IR e immagini multiple. Ecco tre delle intuizioni più interessanti:
Tipica distribuzione longitudinale del flusso di calore
1. Tipica distribuzione longitudinale del flusso termico in un riscaldatore verticale per alimentazione a gas
- Il calore aumenta e raggiunge i picchi verso la fine del focolare (configurazione simmetrica)
- Le temperature superficiali dei tubi più alte si verificano dove normalmente si hanno un alto flusso termico e alte temperature di processo.
Simmetria lungo l’asse di combustione
2. Riscaldatore a cassetta orizzontale con simmetria lungo l’asse di combustione
Il flusso termico aumenta lungo la lunghezza, non raggiunge il massimo alla linea centrale e si sposta verso la regione superiore. Comprendere le caratteristiche dell’attrezzatura è la chiave per le prestazioni del forno. Questo aiuta gli specialisti della temperatura di WIKA a capire le migliori posizioni per ogni singolo test. Illustra anche come ogni forno dei nostri clienti sia unico. Tutte queste variazioni richiedono un alto livello di competenza del forno per ottenere il massimo da un sistema di monitoraggio della temperatura.
3. Tipica distribuzione del flusso termico circonferenziale in un tubo sottoposto a combustione da un solo lato
- Il calore aumenta e raggiunge i picchi verso la linea centrale del tubo (configurazione simmetrica per i tubi rivolti verso la fiamma)
- Sul tubo, le più alte temperature superficiali normalmente si trovano dove si verifica un alto flusso termico e alte temperature di processo
- La posizione spaziale e circonferenziale è importante quando si posiziona la termocoppia.
I clienti: Il cuore del business WIKA
WIKA è un leader mondiale nella strumentazione, ma l’azienda è più che produttore di semplici prodotti. Dopo tutto, sensori e misuratori da soli non soddisfano le esigenze dei clienti. Il nostro obiettivo è quello di applicare i nostri prodotti per risolvere problemi difficili e fornire soluzioni di lunga durata. Siamo il vostro partner focalizzato sull’applicazione.
Questa nuova struttura di test nella zona di Houston è semplicemente l’ultimo passo verso il nostro obiettivo di anticipare e soddisfare le esigenze degli utenti finali. I risultati di laboratorio hanno il loro posto e sono sufficienti per molte applicazioni. Tuttavia, per le applicazioni oil & gas i test in condizioni reali in un’unità di processo funzionante a grandezza naturale producono i dati più affidabili. Ancora più importante, ora possiamo replicare (non solo simulare) i vostri problemi, e poi ottimizzare le soluzioni.