Quali sono gli errori nei sistemi di dosaggio? Le indicazioni dei tecnici della società CELMI srl, da oltre 40 anni impegnata nella produzione e vendita di sistemi di pesatura industriale, vi aiuteranno ad ottenere misurazioni sempre precise, calcolando tutti gli errori durante le procedure.
Ogni sistema presenta la possibilità di generare errori e anche i sistemi di dosaggio non ne sono esenti. Esistono, tuttavia, modi per azzerare tali errori così da poter ottenere dosaggi sempre precisi e affidabili. Per iniziare, è opportuno fare una distinzione tra due tipologie di errore: gli errori di misura e gli errori di controllo, rispettivamente causati dalle strumentazioni e dalle caratteristiche dei macchinari. L’analisi degli errori è assimilabile alle stesse procedure valide per i sistemi di pesatura.
ERRORI DI MISURA NEI SISTEMI DI DOSAGGIO
∙ Tolleranza dell’uscita nominale delle celle: solitamente trascurato nei sistemi di dosaggio, è necessario considerarlo se viene richieste un’alta precisione e si compensa con una taratura degli angoli;
∙ Errore di linearità delle celle: è dato dal peso di ogni componente e dalla sua posizione nel campo di misura; se la pesatura avviene al centro del campo di misura, l’errore sarà nullo; più ci si avvicina agli estremi del campo, maggiore sarà l’errore;
∙ Errore di isteresi: nei dosaggi in scarica utilizzare la linearità in discesa che è data dalla differenza tra linearità e isteresi;
∙ Deriva sotto carico: il peso viene acquisito istantaneamente, quindi non è da considerarsi;
∙ Risoluzione della misura: considerata in tutte le applicazioni;
∙ Errore di ripetibilità: va calcolato considerando il peso di ogni singolo componente da caricare;
∙ Stabilità del convertitore A/D: da non considerare in quanto contenuto all’interno della risoluzione;
∙ Derive termiche di zero: con l’azzeramento prima di iniziare la carica di ciascun componente non è da considerare;
∙ Derive termiche di campo: considerate in base al peso di ogni componente da caricare.
GLI ERRORI DI CONTROLLO NEI SISTEMI DI DOSAGGIO
A parità di condizioni, gli errori di controllo in un sistema di dosaggio sono dati dalla velocità produttiva. A maggiore velocità corrisponde una minore precisione. Le cause principali degli errori di controllo sono:
∙ Il tempo di risposta della strumentazione, per quanto breve possa essere, è un valore definito e può incidere in maniera rilevante per cicli di dosaggio molto brevi; il tempo di risposta è la differenza di tempo tra l’istante in cui il peso supera il valore impostato e l’istante in cui lo strumento emette il comando di intervento.
∙ Il tempo di arresto della macchina di alimentazione del componente durante il quale una certa quantità di materiale, non ancora pesato, continua ad alimentare la quantità dosata;
∙ Il materiale in caduta tra la macchina di alimentazione ed il materiale in tramoggia al momento dell’arresto; ∙ L’errore totale risultante dalla somma degli errori sopra indicati, e fortemente influenzato dalla portata di alimentazione il che giustifica quanto detto in precedenza che la maggior velocità determina un maggiore errore nel dosaggio; anticipando l’arresto di una quantità uguale all’errore totale (pari alla somma dei tre errori sopra indicati) si annullerebbe l’errore salvo che la portata di alimentazione non sia costante sia per effetto dell’incapacità di molte macchine di dare una portata volumetrica costante, sia per effetto della variazione di peso specifico del materiale; ne risulta un errore di dosaggio proporzionale alle presumibili variazioni di portata di alimentazione in peso il cui valore è pari alla somma degli errori sopra indicati moltiplicata per la percentuale di incostanza della portata (compresa tra il 5 ed il 20% a seconda del tipo di materiale e di macchina adottata.
Di seguito, le equazioni per eseguire i calcoli degli errori:
∙ Il tempo di risposta della strumentazione: Qs = Fe * ts
∙ Il tempo di arresto della macchina di alimentazione: Qa = (Fe / 2) * te
∙ Il materiale in caduta tra la macchina di alimentazione ed il materiale in tramoggia: Qc = 0,34 * Fe * √H
∙ L’errore totale: ED = EV * Fe * (ts + (te / 2) + 0,34 * √H
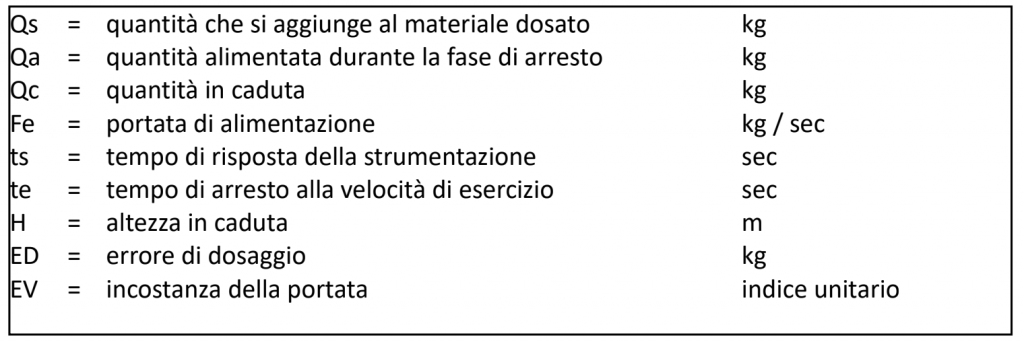
PRECISIONE DI TARATURA
Tutti i sistemi di misura hanno una precisione relativa a una retta di taratura ideale che non sempre corrisponde al vero valore di taratura. La differenza tra la retta ideale e il vero valore di taratura è definito, appunto, errore di taratura. Per capire, ecco due esempi:
1. una bilancia molto precisa (0,1%) ma tarata con un errore del +10% darà sempre misure molto diverse dal valore vero (errore di misura compreso tra +9,9 e +10,1%)
2. una bilancia poco precisa (2%) ma tarata esattamente sul valore vero darà misure più precise (errore di misura compreso tra -2% e +2%)
La scelta del metodo di taratura ha il fine di ridurre l’errore di taratura compatibilmente con l’onerosità delle operazioni di taratura.
PROBLEMI MECCANICI
Le procedure di taratura dei sistemi di pesatura negli impianti industriali incontrano spesso delle problematiche. In particolare, le problematiche si dividono in relazione a:
∙ Sistemi statici: usare pesi campione è estremamente onerosa per portate di fondo scala elevate a causa dei posizionamenti stessi dei sili, solitamente inseriti negli impianti rendendo difficoltosa la movimentazione di grossi carichi;
∙ Sistemi dinamici: usare materiale per la taratura richiede la movimentazione di grandi quantità di materiale; solitamente le bilance a nastro sono posizionate in luoghi difficili da raggiungere;
Esiste la possibilità di impiegare metodi di taratura simulati, meno onerosi ma che rendono necessario un azzeramento degli errori meccanici, cosa possibile solo attraverso un’installazione impeccabile. Tra gli elementi meccanici che influiscono sugli errori nei sistemi di pesatura, generalmente, sono annoverati:
∙ l montaggio delle celle di carico non perfettamente verticale
∙ Le dilatazioni termiche differenziali tra parte pesata ed appoggi
∙ I vincoli orizzontali che introducono un carico verticale che viene sottratto alla pesatura ∙ Tubazioni o altri organi di carico e scarico del materiale in tramoggia che se non svincolati opportunamente possono interferire sulla misura del peso
∙ La poca rigidità del piano di appoggio della tramoggia.
Per ricevere maggiori informazioni e dettagli sui sistemi di pesatura industriale prodotti e venduti da Celmi srl, visitate il sito www.celmi.com e scriveteci a info@celmi.com